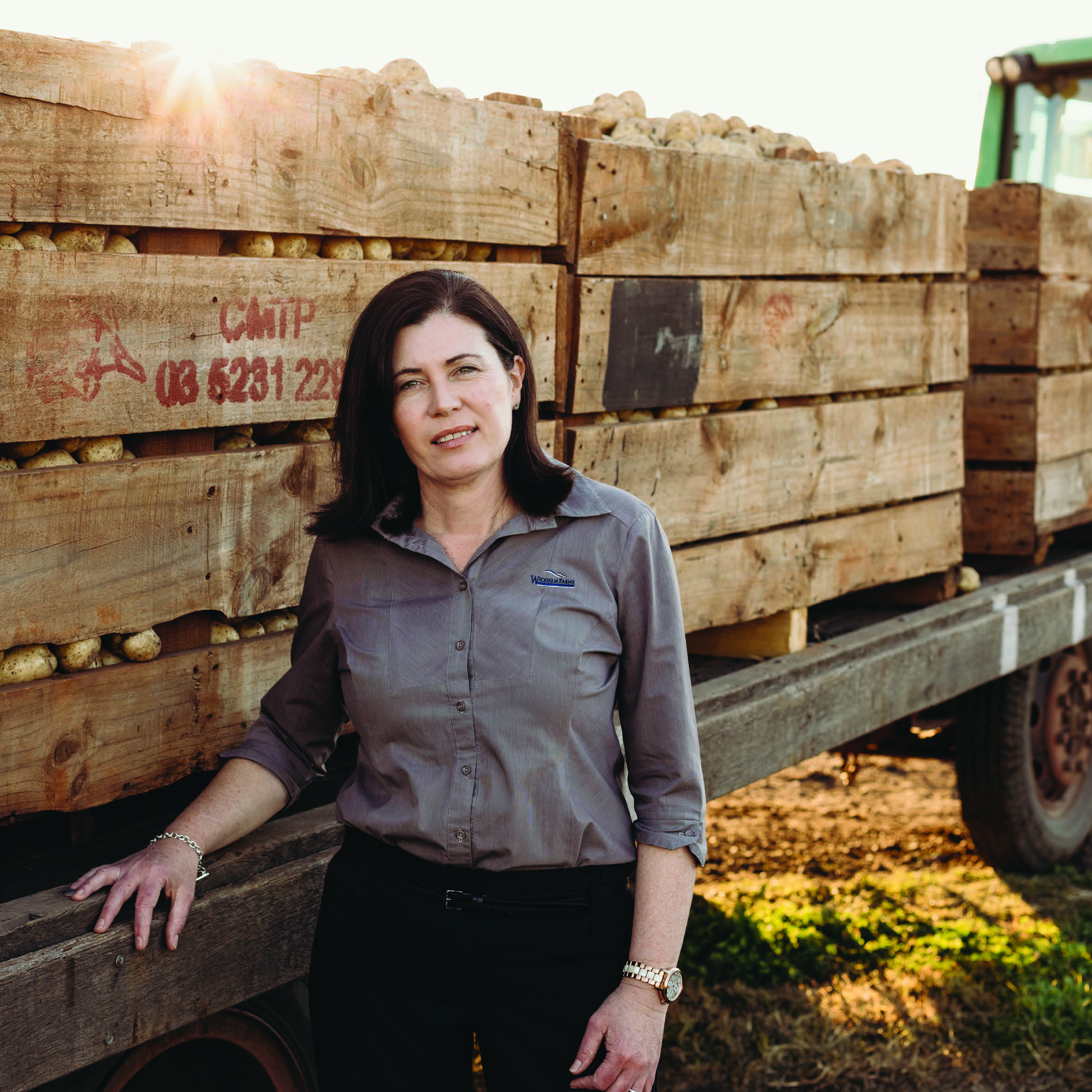
International Business Innovation Mentoring benefits Wickham Farms
28 September 2023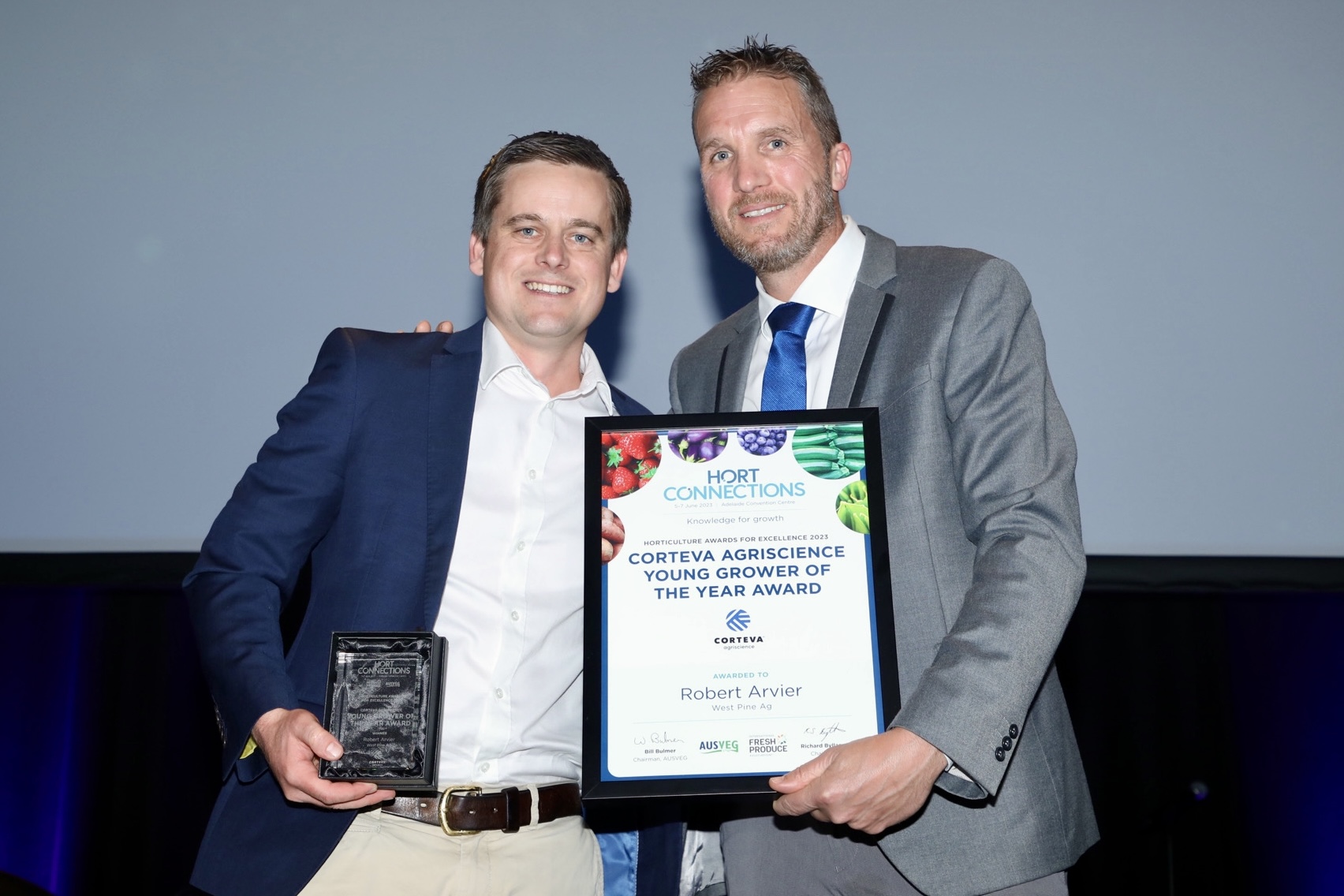
Hort Connections 2023 Young Grower of the Year
28 September 2023Creating a more efficient and productive business for agriculture has become increasingly urgent with rising input costs and labour shortages. Understanding where improvements can be made, and finding the source of the problem using Lean principles will strengthen a grower’s business outlook.
Inefficiencies such as using too much fertiliser at the wrong time, is a relatively obvious point of waste that can cost a grower both in expenditure for the fertiliser, and also affect yield and product quality.
How often though is one machine turned off to clean out a blocked shute? How much productive time is lost when perhaps a re-think of how an onion enters that shute might prevent this regular occurrence?
The principles behind Lean management can give strategies on how to understand where the bottlenecks in a business occur and provide a means of rectifying a problem at its source. With appropriate training and communication, issues such as the blocked shute can be highlighted much earlier and a solution found.
Developed in Japan by Toyota Motor Corporation, Lean is a business management tool designed to utilise resources more efficiently – including materials and workforce – and reduce wasteful practices. While originally used in manufacturing, the principles can be applied to many aspects of agriculture, both in the field and in the packing shed.
The key elements of Lean are to:
- Eliminate Waste: does it add value to your business or your customer? By removing elements that not adding value, can reduce input costs and reduce wasted resources;
- Quality: ensuring that the businesses are producing products to a consistent standard reduces off-spec product, and improving systems to ensure consistency;
- Training: ensuring that all staff understand how a system or process works and providing the necessary training documents that give a consistent outcome, regardless of who is operating the machine or operation;
- Continuous improvement: improving your business is a constant process to fine tune systems and processes;
- Business culture: by engaging all staff in the Lean principles means that everyone feels a part of the goals and works together to achieve that outcome.
Bringing Lean into the onion packing shed
A chance opportunity to see a presentation by Greg Lane, who was a key person with Toyota in North America for Lean principles, gave Charlton Farm Produce Managing Director, Mark Addison the light bulb moment to improve the family business.
Further reading, a training course online and a chance to undertake a Simulated Work Environment in Burnie to understand how Lean principles worked, enabled Mark to see how Lean could be implemented at least in the onion packing shed.
For Mark, key drivers for implementing Lean are to improve efficiency in the business, from how staff move around the packing shed, to improving how grading is achieved to minimise waste.
“One of the biggest things I have learned is that too many times, I looked at a problem to fix, without understanding the root cause of the problem,” said Mark.
“So fixing that problem, may not actually make any difference – Lean makes you look beyond the problem and find a solution that gives a better longer term outcome.”
The Lean principles may have originated in a manufacturing environment, but it is clear that even in the field, it can be applied.
“When we look at a crop, understanding the conditions that influenced its growth – weather, irrigation strategies, changes in fertiliser application – all that information can help us fine tune what we do next time.
“With that in mind, we can upgrade our training and documentation, so that staff know what to do and understand what the end goal is. While every season can vary, it means we have a better idea of what needs to be done so we are not wasting as much time and effort later on.”
Three years into Lean, Charlton Farm Produce is now seeing the benefits in the packing shed with productivity increasing, and less wastage in produce.
One aim was to reduce the number of shifts operating. By looking at the processes through a Lean lens, bottlenecks were identified within the packing shed and improvements to workflow gave higher productivity through the equipment, doubling production. In addition, less damage is occurring to the onions giving more saleable grades and less waste. Training staff on the changes made to the packing shed has also been a benefit.
“I try do every job in the business at least once a year, so I can see what it is like to be in someone else’s shoes. What that gives me is a perspective of what can be improved, how the equipment is performing and what training needs to occur to help the operator and the process perform better.
“For example if a machine is not performing optimally, and the operator is not aware that it could be better, it doesn’t get reported. Get the machine fixed, re-train and encourage staff to raise any issues they see. Knowing what it should be doing means that all elements of the packing shed are assessed and improved.
“One of the biggest realisations I had was how training documentation was presented. A lot of what I had written was very wordy – changing it to a more visual representation and attached to the equipment made it a lot easier for operators to understand what to do, and it is readily accessible.”
For any horticulture business, labour is one of the largest cost components, which means it has the potential for the biggest gains under Lean. Simple changes to workflow in the packing shed so that a supervisor is not walking from one side to the other to push a button when it could be done automatically are an example of how Lean can improve productivity.
“One of the reasons we went down this path, was based on concerns around costs and our markets and trying to get ahead. Lean gave an opportunity to smarten up the business and we now have a vision of long term financial viability, which had not been there before.
“Lean has taken our business from uncertainty to a confident future.”